Carbonisation
A Unique Process – Continuous Tire Pyrolysis Technology & Systems
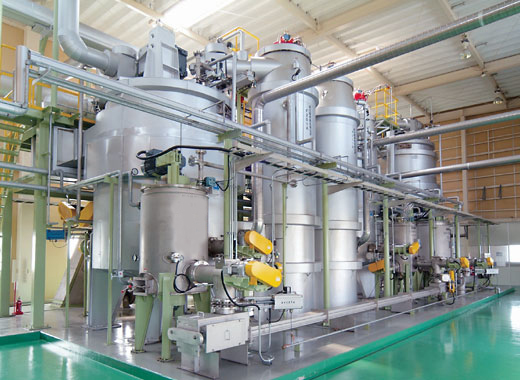
Unique continuous Tire Pyrolysis Technology & System.
A unique feature of our carbonization process is the fact that we do not need to shred the spent tire casings we can process them in whole form which significantly reduces our capex, processing, operating and maintenance costs. The tires are to the top of the kiln and dropped down through a vertical feed system that continuously feeds the kiln and is computer controlled. This is achieved using a series of alternatively sealed, gravity feed, control valves that feed and transportation the feedstock through vertical process chamber. The process is operated under precise continuous digital monitoring and no heat or vapors escape through the feeding system. Our pyrolysis creates zero waste and produces no more emission than a natural gas boiler.
Oil is produce through the condensation of the produced hot syn-gases. These hot gases are passed through a catalytic converter that reshapes the syn-gases into the desired chain length molecules and cools and condenses these gases into the desired oil product there is some flexibility in the type of oils produced and this can be customized to meet project requirements. A small portion of the syn-gases will not reshape or condense into oil and these syn-gases are then removed and filtered out of the process and are thermally oxidized to produce the plant process heat. The use of these non-condensable syn-gases eliminates the need for outside fuel to power the process. It also eliminates the need to store these gases on site which would add to the plants capital cost and permitting times. The remaining high grade oil is sold in the open market to our industrial customers on long term contracts. We also have the option to blend the oil product with biodiesel which is then eligible for a tax credit under the Renewable Portfolio Standards (RPS). The oil can also be used as a blending feedstock with other petroleum fuels and can also be used as chemical feed stock for the production of new polymers. The system is fully automated and is operated under precision computerized control systems for quality control.
The steel and raw carbon char are conveyed to the magnetic separators where the steel is removed and briquetted. The steel is then sold to steel smelters and rebar manufacturers and is completely recycled. The carbon char is then upgraded to carbon black using a proprietary process that creates carbon black that meets quality specifications required by rubber and plastic manufacturers. An onsite laboratory monitors the production process so that the carbon always meets or exceeds the exact product specifications for our customers. Once the process is complete the carbon black is pelletized and stored in super sacs for shipment to customers.
PYROLYSIS & CARBONIZATION IS NOT INCINERATION
Pyrolysis does not involve the burning or combustion of any feedstock, let alone scrap tires. Pyrolysis is the thermal break down of carbon based materials under controlled conditions in the absence of oxygen (less than 1%), whereby the material chemically decomposes into its constituent elements without burning or combustion.
Mobius pyrolysis process involves feeding whole tires into a vertical kiln that is indirectly heated at low temperatures to convert and pyrolysize the tires under inert atmosphere. The tires are thermally decomposed without burning into oil, gas, carbon char and steel. There is no combustion or incineration of tires during the process, what so ever.
Super Clean Web 2.0 WordPress Business Template - Debonair WordPress Theme created by Artivity exclusively for ThemeForest.