Environmental Impact
Maximizing the Efficiencies of Green Technologies to Extend the Life of Finite Resources
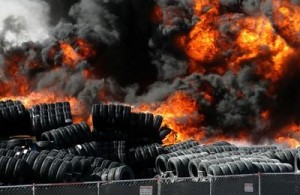
Stockpiled tire fires destory our natural habitat for decades
Over 75% of the cost of a tire goes into the construction and building of the tire casing which is the main component that keeps your tire on your wheel/rim and gives it strength and durability. That being said , it only makes sense to keep a tire, a tire for as long as possible and thats what we do at Mobius. In the simplest of terms the tire that are not suitable to be remanufactured and put back on the road as a new tires will be processed and recycled using Mobius’s thermal depolymerization technology or what is commonly known as carbonization.
This technology essentially melts down scrap rubbers tires and polymers into their original components. We use heat in an oxygen starved environment to thermal “crack” the polymeric materials back to oil and gas. The remaining solid materials consist principally of the original carbon black materials, which are recovered in a process that retains their reactivity properties and usefulness in rubber products. Subsequent upgrading in a patented refining process assures the production of an effective carbon black reinforcing and tinting material that is available commercially today called CBk.
Mobius technology is unique in that it is currently the only system worldwide that can process both whole (unprocessed) tires and can also take shredded feedstock as well in a controlled environment (less preprocessing reduces costs). The collected syn-gas (vapor), oil and solid carbon residuals are high grade finished end products. This process takes place in s sealed vertical reactor and is operated responsibly using digital telemetry based PLC computer systems under strict industrial protocols that exceed all regulatory standards.
Two of the main end products are usable as fuels, an oil and syn-gas. The syn-gas has high thermal value and is used as process heat for fueling the system after initial start-up. It can also be diverted for use elsewhere as a boiler fuel or to generate electricity, depending on the configuration of the facility. For each tire processed, in approximately one gallon of oil is generated, with properties similar to a diesel fuel. This oil is sold as an industrial fuel oil, or is refined to a transportation grade fuel. The result of recycling end-of-life rubber materials is the recovery of the raw materials that were used to produce the products in the first place: oil, gas and reinforcing carbon.
Impact on Landfills
Mobius estimates the current market potential for recovered reinforcing materials to exceed 500 million kilograms in the United States alone upgrading the current utilization of scrap tires to higher economic value is not rocket science. Based on the above less than ¼ of the scrap tire generated annually would be consumed, virtually eliminating the need for landfills and provide and incentive for the remediation of existing tire dumps and the “mining” of scrap tire mono-fill landfills. Landfilling oil is simply stupid.
The environmental impact of scrap tires is significantly reduced:
- Reduction of landfilled scrap tires
- Reduction of oil use to generate carbon black
- Reduction of CO2 emissions
A Secure Domestic Source of Energy
An obvious solution for reducing the North America’s dependence on foreign oil could be achieved by:
- Using thermal de-polymerization technologies for processing scrap rubber and tires into oil makes sense both environmentally and economically. For every tire recycled through the Mobius process over one gallon per tire can be recovered. Assuming a ¼ of the annual scrap tires could ultimately be processed using the Mobius solution, approximately of 500 million litres of oil would re-enter the industrial marketplace.
- The current carbon black products used in rubber products are predominantly produced by the incomplete combustion of fuel oil to create carbon black (analogous to the production of “lamp soot”). Based on US Census Bureau data, it is estimated that 1.5 litres of oil is used to produce one kilogram of carbon black. Based on this estimate, approximately 400 million litres of oil would be saved by using Mobius CBk reinforcing carbon black to avoid production of new carbon black.
Offsetting Carbon Dioxide Emissions
The production of new carbon black using fuel oils is estimated to generate an approximately a kilogram of CO2 per kilogram of carbon black produced. To produce 1 ton of virgin CB requires 2 tons of heavy oil and produces 10 tons of CO2 (including fuel acquisition).
In contrast, the recovery of carbon black using the Mobius system is estimated to generate a total of 0.25 kilograms of CO2 per kilogram of CBk carbon black produced, offering the environment an approximate net reduction of 0.75 kilograms CO2 per kilogram of carbon black produced. The end result would be annual CO2 offsets in excess of 500,000 tonnes just in the United States alone.
Facts:
- Using the recover materials from the Mobius process would have positive impact on the environment
- Result in the virtual elimination of scrap tire landfills
- Annual oil savings of oil use in excess of 400 million litres in the United States alone
- CO2 offsets of approximately 500 thousand tonnes per annum in the US.
- Using 1 tonnes of CBk would prevent approximately 400 tires from going to landfill
- Every tonne of CBk used would offset the need to import approximately 3000 litres of oil
- Every tonne of CBk used would offset approximately 750 kilograms of CO2 emissions
Super Clean Web 2.0 WordPress Business Template - Debonair WordPress Theme created by Artivity exclusively for ThemeForest.